Featuring cultural performances, exhibits, and culinary delights, RACV is proud to be partnering with Melbourne Diwali for the RACV Melbourne Diwali 2024 festival, which promises to be a great free event for the whole family.
How the car industry is helping the fight against COVID-19
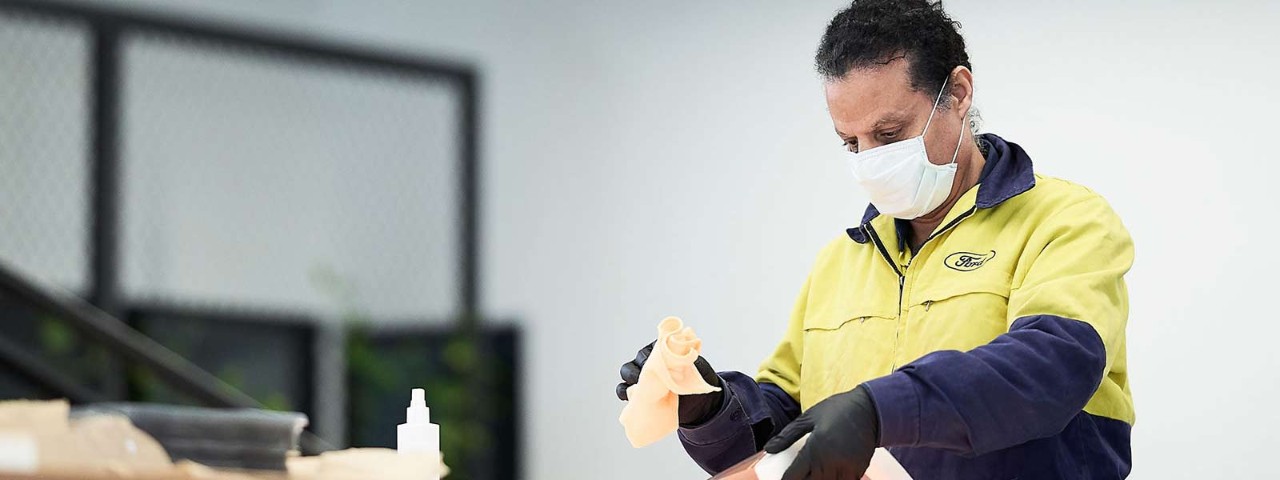
The car industry is helping front-line services fight COVID-19. Here’s how.
Across the globe and here in Australia, the automotive industry has joined the fight against COVID-19, lending engineering smarts and manufacturing capacity to provide vital equipment for those working on the front line.
In Italy, one of the worst-hit countries, supercar manufacturer Lamborghini has begun producing surgical masks and protective plexiglass shields to donate to a nearby Bologna hospital, while Ferrari and Fiat Chrysler are talking with the country’s largest ventilator manufacturer, Siare Engineering, about helping to expand production.
In the US, Ford Motor Company is working to boost manufacturing of 3M’s powered air-purifying respirator designs, and is looking at using off-the-shelf parts such as fans from the Ford F-150’s cooled seats for airflow to speed production. And General Motors has deployed 1000 employees to build critical-care ventilators at its factory in Kokomo, Indiana. GM and Fiat Chrysler’s US outpost are also producing medical face masks.
The local effort
While we no longer actually make cars in Australia, our automotive industry has retained a strong design and engineering presence, which is rallying to the cause.
With the Australian 2020 V8 Supercar series on hold, the Erebus Motorsport team has shifted focus at its Dandenong workshop to produce full-face masks and a protective Perspex box designed to shield healthcare workers from infected patients.
The box, which fits over a patient’s chest and neck, with holes where doctors can insert their hands, was designed together with Supercars medical delegate Dr Carl Le. He says the box provides an additional physical barrier for doctors when a critically ill patient needs to be intubated. “That’s one of the riskiest times for a healthcare worker because they must be in very close proximity to the patient.”
The apparatus is being trialled at two Melbourne hospitals and Erebus says it can produce 20 units a day if needed. The Erebus team is also working with Carl on a new solution for two-way communication in and out of isolation rooms.
Erebus isn’t the only Supercars outfit using the racing hiatus to help the cause. Red Bull 888 Holden Racing Team has designed and engineered a prototype ventilator that it says can be used wherever and whenever it’s needed. Red Bull has made its design ‘open source’, allowing authorities around the world to adapt and use to suit their own requirements.
Meanwhile in Clayton, Holden Special Vehicles’ (HSV) parent company Walkinshaw Automotive Group has set up a dedicated team to support health authorities and potentially individual hospitals during the COVID-19 crisis.
Walkinshaw director Ryan Walkinshaw says the team has already responded to a government request to produce personal protective equipment (PPE), specifically face visors, but is also exploring other products that might help health authorities.
“We see this as a way we can help Australia during a tough time and relieve some of the burden on the health workers who will no doubt need as much help as they can get in order to get through this the best way possible,” he says.
Ford Australia, which remains one of the local automotive industry’s largest employers despite the 2016 closure of its Broadmeadows and Geelong manufacturing plants, has put forward its local engineering expertise to help out.
Ford says it will produce and donate up to 100,000 face shields for frontline healthcare workers, using production cells at its Broadmeadows facility. It has already produced 50,000 shields and it is liaising with government about the ongoing need for PPE.
The company has worked with several local suppliers to procure materials for the face shields. Prototype shields were tested in five Victorian hospitals.
Toyota Australia’s product planning and development team have designed and prototyped face shields that are being produced at the company’s Port Melbourne facility. They are currently being delivered to various hospitals around Melbourne free of charge.
Toyota says it has the materials and labour to produce about 2000 face shields initially, but this volume could be scaled up significantly with the help of manufacturing partners and suppliers. The production line can currently produce one face shield every minute.
The Australian Automotive Aftermarket Association has also offered the services of the Auto Innovation Centre (AIC) in Mulgrave. The AIC has already produced prototype medical parts using 3D-printing technology – also known as additive manufacturing.
AIC managing director Luke Truskinger says while it is encouraging that the industry is offering assistance during the pandemic, the efforts needed a more coordinated approach.
“The time is right to bring everyone together to coordinate the industry, health departments, and governments on what should be produced as a priority,” he says.
“Coordinating the approach can optimise the best use of the industry and ensure the best result for all. Considering the state of emergency this could just be agreement on designs and a verbal understanding of any cost coverage for the companies so they know how far they can push their resources beyond their current allowances.”
Automotive electronics manufacturer Redarc is also in early talks with government about shifting the focus of some of its production to electronic circuit boards for ventilators.